Cooperation between Marine Support AS and EW Production
From Idea to ready approved 19000m3 MGO storage / fueling facility. All done by full prefab package projected, designed and produced by EW Production OU. Local overall projected, officially approval handling and xxxxxx in cooperation with Marine Support AS, Norway.
By use of prefabrication and simultaneously site preparation and tank production the total time frame from signing of project to ready approved facilities can be reduced by 50%. This will in many cases be an attractive solution for our clients due to less potential administration on site, less sensitive to weather conditions and rapid cashflow and hereby return of investment.
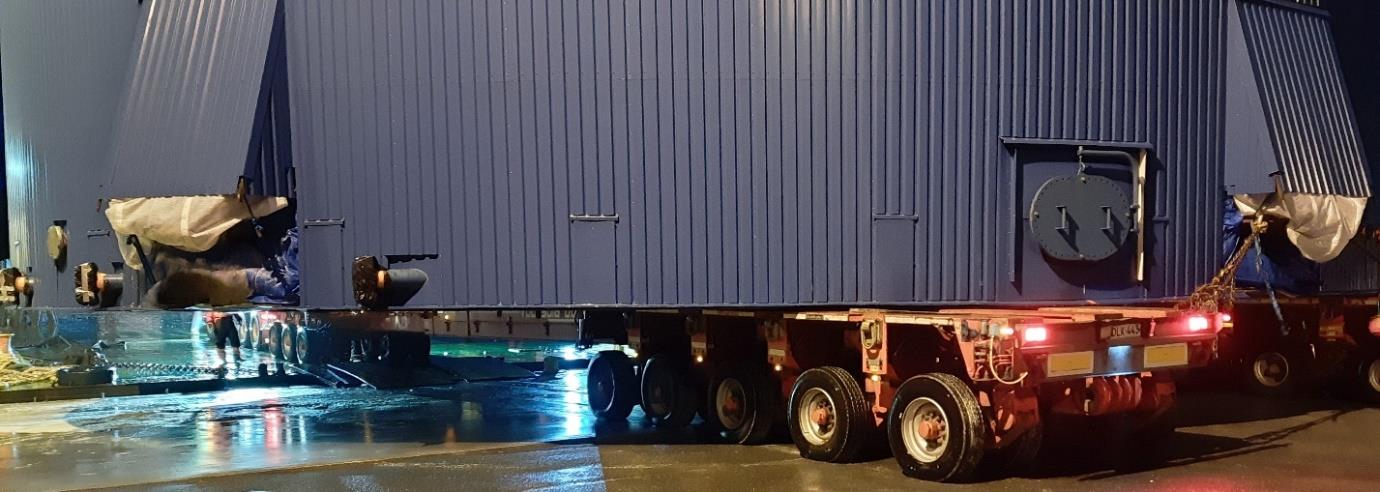
Process:
Talks regarding expected total volume and information of available ground area.
Production of initially idea and possible GA layout and method of shipping.
Two options were considered: constructing the reservoirs on-site or transporting pre-fabricated tanks. After a thorough site visit and evaluation of various possibilities, the decision was made to prefer the delivery of ready tanks.
Application and Approval from local authorities.
Based on the GA design and other issued documentation, applications is send to the respective official authorities for approval of full building precision and approval of tanks solution. Also multiply other tasks like risk analyses and environmental impact is carried out.
A strong HSE (health, Environmental, Safety) project platform is approved and implemented. Special permission for cranes and other equipment is granted and staff is trained.
Design lock and signing of production planning.
Tanks
1 x 1000m3 capacity (with a diameter of 10m and a height of 12m)
3 x 6000m3 capacity. The larger tanks had a diameter and height of 20m each
Method of production was decided to Prefab and unit shipping by vessel.
Design and approval of Pipe and flow system.
3D Models and drawings is produced, the full pipe systems is designed to fit the landscape of the local site. EW engineers will visit site to gain the nessasary information in order to create 3D model.
Start of Local works on site and start of prefab tank building simultaneously.
During the engineering and calculations, significant attention was given to the craning and jacking of the tanks post-construction in Estonia and before the actual installation at the terminal in Norway. Multiple simulations were conducted to confirm the structural strength. Once the basic parameters were agreed upon with the customer, detailed engineering and the production of necessary documentation for third-party approvals were carried out.
Building of tanks is started on the EW Production site in Estonia.
Ground works, concrete foundation and leakage ring wall construction is started on site in Ålesund Norway.
Design and approval of Pipe and flow system.
3D Models and drawings is produced, the full pipe systems is designed to fit the landscape of the local site. EW engineers will visit site to gain the nessasary information in order to create 3D model.
All pipes, pipe support and pump house is started. Pumphouse is delivered as a complete container frame-based solution, pipes is delivered with welded and approved flanges. All pipe supports are delivered ready hot galvanized.
Test and approval of tanks on building site in Estonia.
The construction of such large tanks was executed using the sheet-by-sheet method. Horizontal welding was performed using a welding robot (welding process 121), while vertical welds were manually executed using the 135-136 welding process. Comprehensive non-destructive testing (NDT) was conducted throughout the building process, with a third- party inspector overseeing the project from the first metal sheet to the final centimeter of welding.
After the tanks are completed the construction “as a hole” is tested by 3 party and finally water filled for final test.

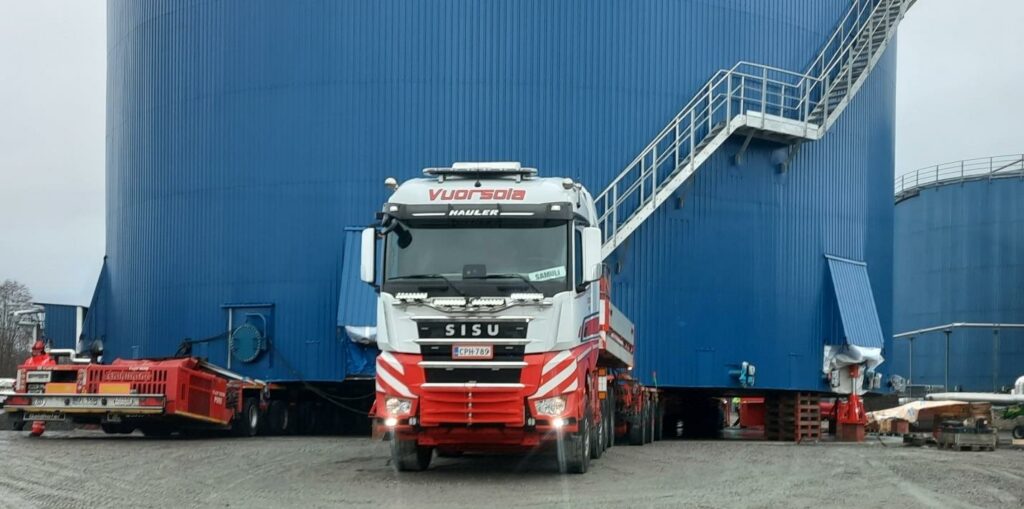
Shipping of tank, pipe system, and pump house preinstalled frames.
Loading these substantial structures is treated as a standalone project internally in EW. A 750-ton crawling crane was mobilized to the harbor, arriving on 30 trucks and assembled on building site. A special temporary road is constructed to safeguard the quays during loading. Finally the tanks is safely secured to the vessel by a crew of stevedores and welders. All monitored approved third party body.
Unloading and positioning onto foundations in Ålesund were carried out using self-propelled modular transporters (SPMT) and hydro jacks. Tanks were driven to their final position, rested on built towers, and then lowered using jacks. The unloading process on-site took three days.
Installation and pretest of all equipment.
Tanks is placed, pipe systems, pump house and automatization is installed, all is carefully visually inspected by multiply bodies. All by law enforced approvals is performed incl. pressure and flow test is performed.
Final approval of installation.
Final as build documentation is issued, the installation is recalculated and finally approval by local authorities. Final commercial approval is issued and commercials can start.